Flashing issues are common in residential construction. During our framing inspections, we try to identify flashing mistakes or areas where there is concern for performance so that they can be corrected early in the construction process. This is often the best time to address flashing issues because often they are visible.
One important flashing detail is the base flashing where masonry veneer siding is supported by the foundation concrete and is a continuation of the water resistant barrier at the base of exterior walls. Base flashing should extend the water resistant barrier over the edge of the foundation as required by current code to prevent water entry to the structure, which can deteriorate the structure. This requires that it is either directly behind the water resistant barrier, or directly adhered to it depending upon whether the builder is using a sheet style water resistant barrier or one integrated to the sheathing respectively.
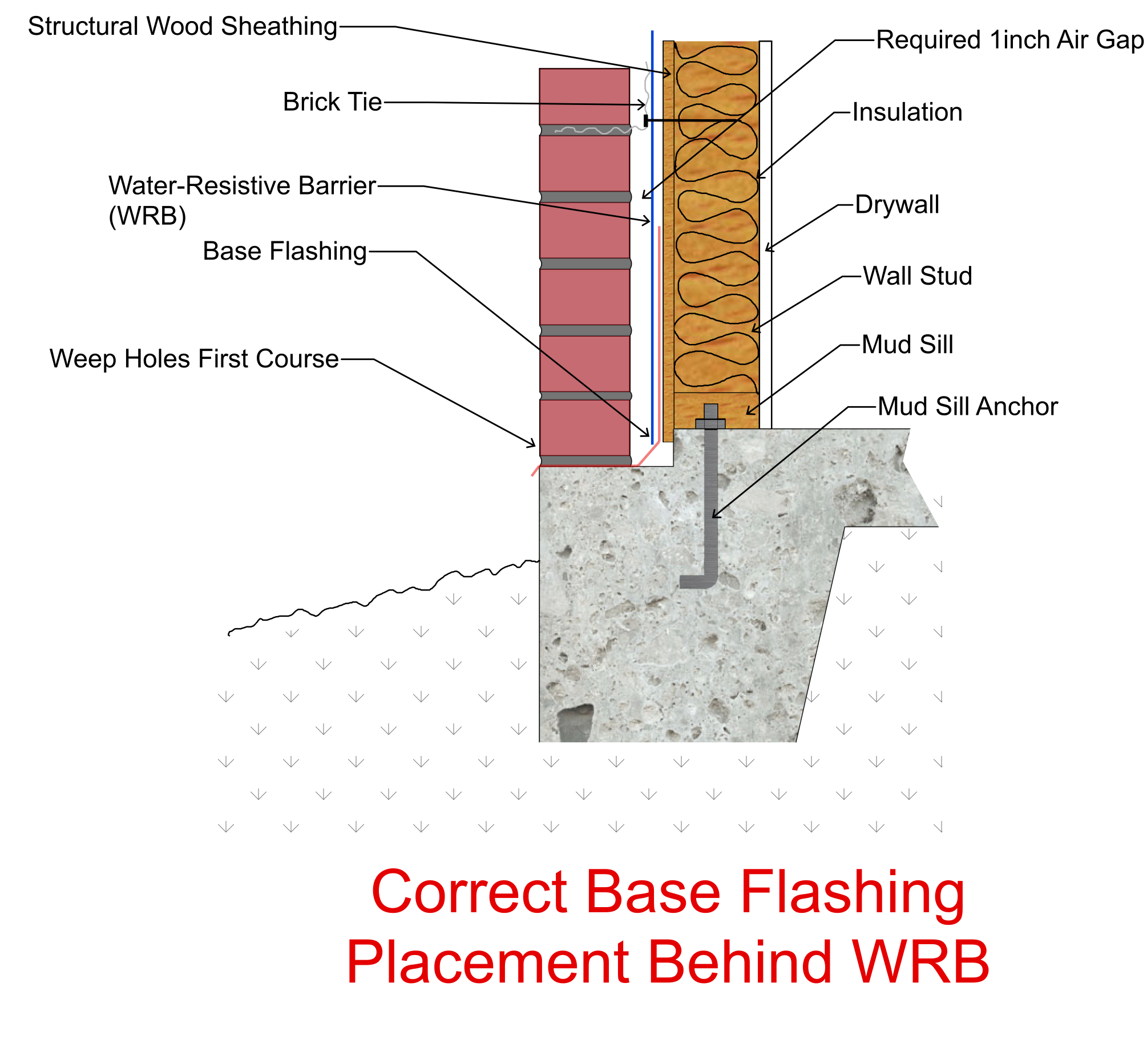
Most often the masonry is stone veneer or brick veneer directly supported by the foundation. In our area the foundation is typically detailed with an offset, or brick ledge, to reduce the potential for water entry. This ledge is stepped down with a typical depth of 1-1/2 inches from the interior foundation floor surface supporting the structure and finishes. The width of the ledge will vary according to the masonry width and required air gap but is typically 5-1/2 inches for standard brick and is created by a 2×6 board nailed to the forming during construction. Base flashing is required even with a brick ledge, and are reasonable, because the quality of brick application has suffered in recent years. Often the mortar used to apply the brick is applied excessively allowing it to slough into the space behind the brick filling of the brick ledge eliminating its effectiveness.
Errors we commonly see in the application of base flashing are:
- Improper application behind the structural sheathing. – This creates a potential for water to enter and wet the bottom of the sheathing at its connection to the sill plate if it cannot drain rapidly at the base of the brick. This also violates the intent of the construction code. If the sheathing is plywood, OSB, or some paper based engineered sheathings they can deteriorate over a relatively short time, reducing the shear capacity and their ability to hold siding at the lower wall.
- Damage to the flashing material – Often builders use thin Polyethylene plastic, which is easily torn, or they damage the plastic during construction for penetrations through the sheathing and sill plate. Some lower quality plastics may also have a short life as compared to purpose made base flashing materials.
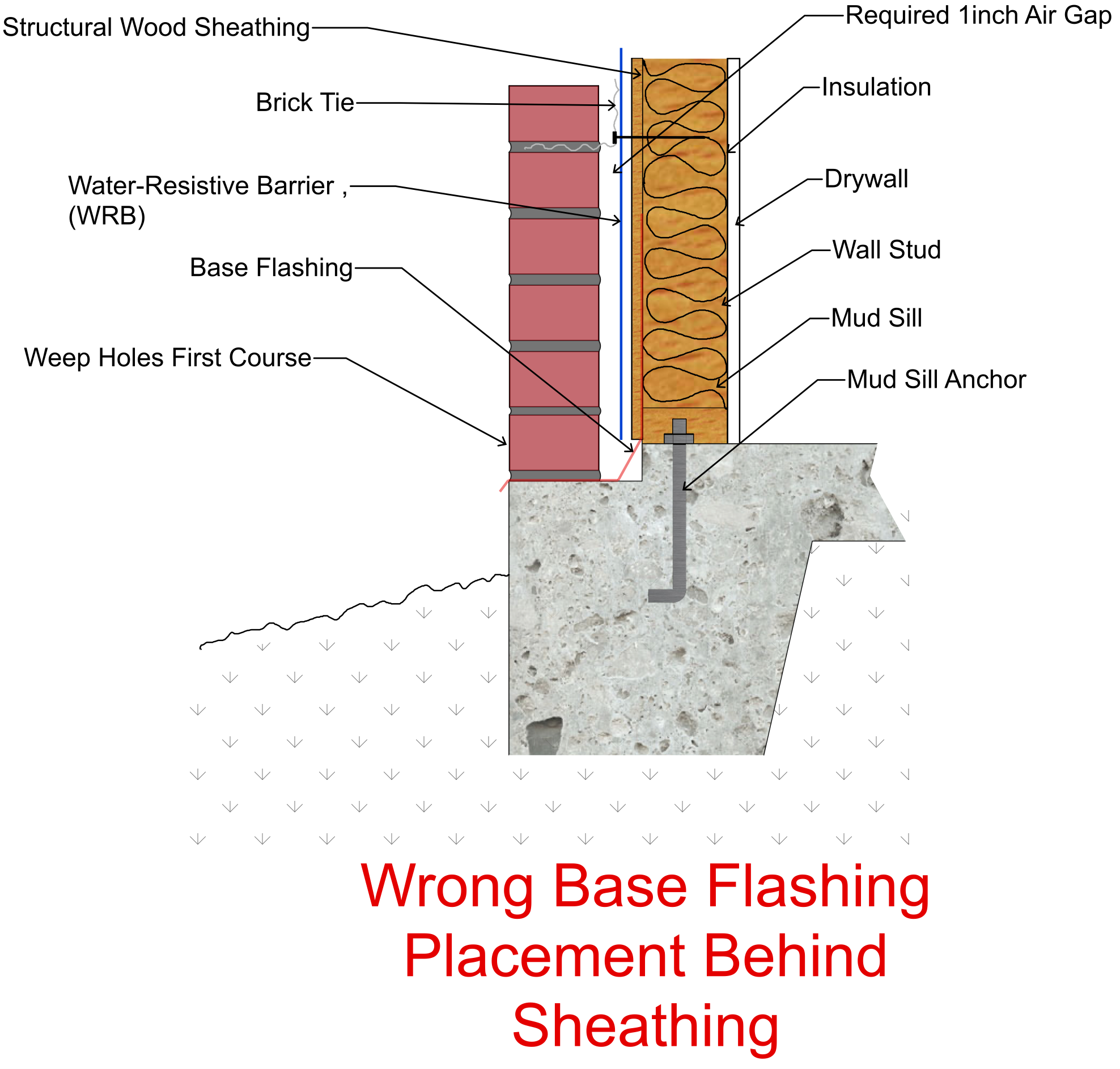
A properly installed base flashing of a good quality material is added protection from water entry over just relying on a brick ledge and is required under the current International Residential Code. These are easily repaired or replaced prior to application of masonry and should be verified by the builder as being properly installed prior to the application of brick.
Recent Comments