Drain Testing-What are the Risks?
Plumbing drain testing has become a common occurrence when purchasing an older home known or suspected to have been built using cast iron for drain lines. In older homes in the Houston area, those built before the 70s, cast iron was commonly used for sanitary sewer drain pipe in both residential and commercial construction. For buildings with foundation resting on the ground the sewer pipes were buried in the soil below the foundation before concrete was placed for the foundation. This makes accessing these pipes for evaluation, service, or replacement costly and more difficult. Since cast iron is known to have an average life expectancy of 40-60 years in our soils and around 70 years above grade the pipe may be ready for replacement in many older homes. Damage to plumbing drains also commonly occurs in buildings having had foundation repairs due to soil movement or as the building is lifted. Testing should always be performed after such repairs.
Although the visible portions of drain pipes may look to be in good condition underground pipes often corrode through from the inside or separate due to movement in the soil or foundation, which often is not visible and results in holes that can leak water or allow root intrusion. When this occurs, it can result in performance problems such as frequent clogging of the drain, permanent collapse and failure to drain, or leaking of water to the soil below grade. Leaks in drains below the foundation can cause problems that result in differential movement in a building’s foundation, creating a need for foundation repair. Testing of older drains can identify these problems early before they result in failure of the drains or damage to the foundation. Homes with cast iron drain systems over 40 years old, or where known repairs or replacement has been performed, are good candidates for testing, and evaluation of the drains should be performed through hydrostatic testing or through camera testing depending upon site conditions and goals. Both tests provide useful but different information although they have some overlap and it may make sense to perform both in some cases.
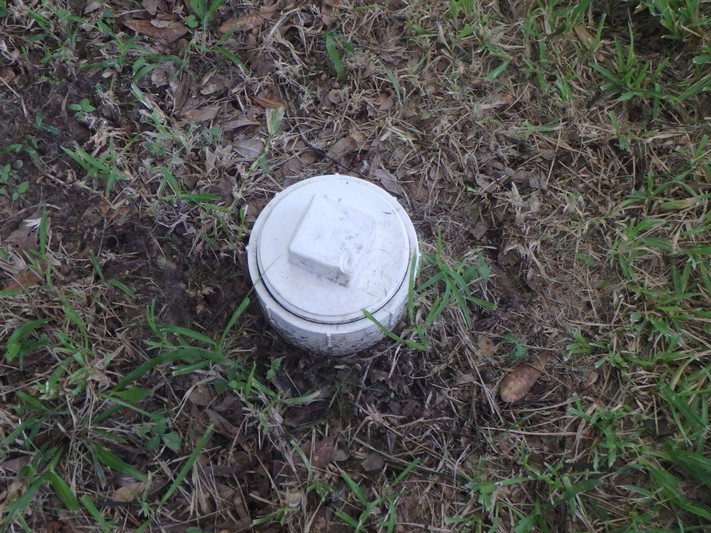
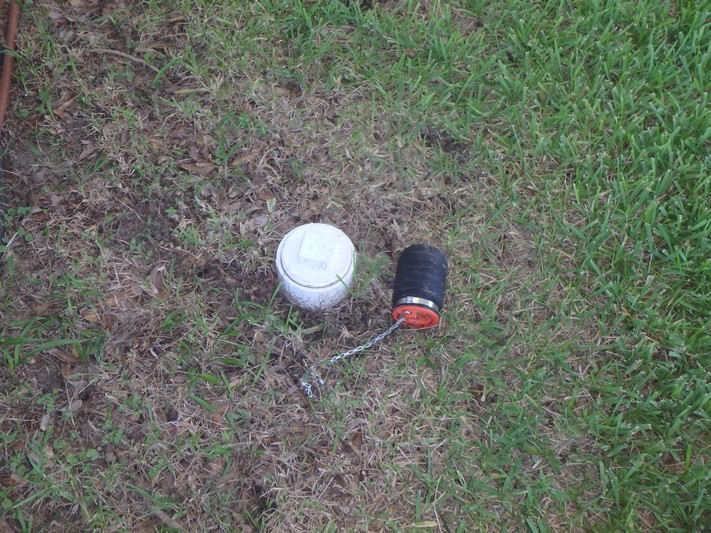

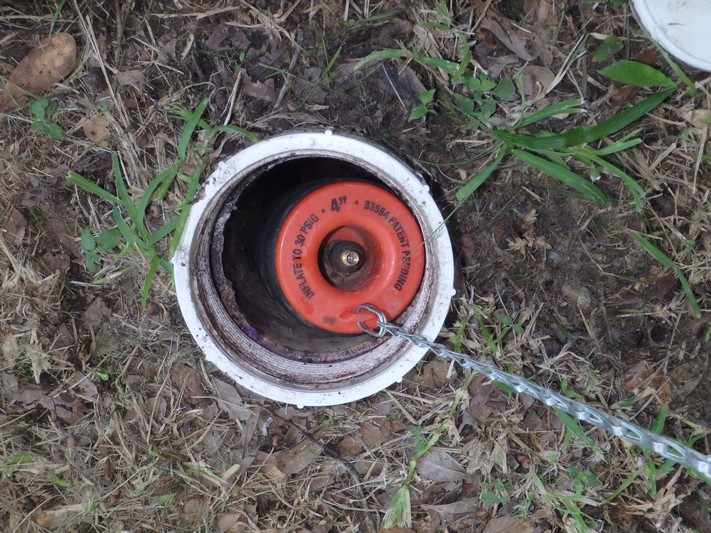
Hydrostatic Testing
Hydrostatic testing is the oldest form of testing plumbing drain systems and is the most common below grade test method as it does not require a lot of special equipment. Hydrostatic testing consists of testing of the drain system using the pressure of a column of water referred to as a “head” of water. Hydrostatic testing is performed from a sewer cleanout in the yard near the building by removing the drain system clean out cover, inserting a test plug to the city side of the cleanout, and filling the drain with water to the height of the cleanout allowing it to stand for a period of time. In some cases where a cleanout does not exist or cannot be located one must be installed or, if possible, testing from a toilet location can be accomplished by removing the toilet from the floor and using the open drain. The water is allowed to stand in the drain for a period of time, typically approximately 30 minutes or more and if the water level drops you know you have a leak in the drain system. This method of testing is considered the most accurate way of finding leaks because it will find very small leaks depending upon how long you run the test. If a leak is detected, then you may elect to use a camera to view the condition of the pipe, to determine where a leak may be likely to exist, and the overall condition of the pipe to determine the value in repair versus replacement. The plumber may also perform an isolation test to determine the specific drain line area or branch where the leak exists.
Isolation Testing
Isolation testing is and extension of hydrostatic testing and is typically performed after a system has failed a system wide hydrostatic test to find the location or area of a leak. If a plumbing drain system were not buried and were laying on the ground it would look a bit like the branches of a tree. Isolation testing blocks the branches in sequence and tests each one for leaks through individual hydrostatic testing until you find the specific branch or area of a branch leaking. This is typically accomplished by pushing a test plug down the drain to block sections of the pipe to allow testing at specific testing. Often a camera is used to assist in locating branches and positioning of test plugs. Isolation testing increases the cost of testing, and in old systems where the entire system is near or at its life expectancy it may not be cost effective since replacement of the entire system would typically be needed in a short time regardless of the outcome or repair in one section of the system.
Dangers of Hydrostatic Testing?
In recent years there has been some concern expressed from home owners and realtors about the potential for damage to the plumbing system caused by hydrostatic pressure used during testing. In Texas this concern has resulted in a requirement for a promulgated standard form from the Texas Real Estate Commission to request permission for testing from the owner and to inform the owner and buyer of the potential for damage to the system. Although there is a potential for damage to components during opening of lines or removal of toilets for testing, the concern for general damage due to testing has largely been overstated. When performed correctly the only pressure used is that of a standing column of water, which can be easily controlled during testing. Although pipe is buried deep as it reaches the city connection most pipe is buried around 3 feet below the slab, which will result in a water column of less than 3 feet in most cases, and 3 feet of water column is equivalent to about 1.3 psi of pressure. If your plumbing cannot hold 1.3 psi of pressure, then it is worn out and should be replaced as it is probable it will see that pressure or greater if the system clogs and fails at the yard under normal performance conditions. Due to the need for removal of components and the requirements of the Texas Real Estate Commission testing of this type should always be discussed with the owner and realtors involved prior to scheduling testing.
Camera Testing
Camera testing is another option to determining the condition of the drain system. Camera evaluation can be less invasive than hydrostatic testing since it often can be performed without removal of fixtures. When camera testing is performed a special camera on the end of a stiff cable is pushed down the drain line taking video as it moves along the pipe. The condition of the pipe and progress of the camera can be monitored in real time by the plumber to allow direct viewing of pipe conditions, branch locations, and other irregularities such as low spots that hold water and solids often referred to as “bellies” or clogs. If a problem is determined to exist it can be quickly located as most cameras have radio position transmitters that can be used by a radio frequency detector carried by hand above the foundation through the building. Most camera systems also provide an indication of the cable length played out during testing providing direct distance readings, which can provide some idea of the distance from the test location. Cameras can also provide real time data on flow patterns when the plumbing is in use that can be used to diagnose flow problems. While cameras do provide more useful information than simple hydrostatic testing they are not as good at detecting leaks and thus have their own purpose. They are excellent for getting immediate feedback on pipe conditions, the conditions at splices and repairs, flow conditions, and are the overall choice of some plumbing contractors when testing is requested because they do show immediate conditions such as severe deterioration often associated with leaks and failure.
Which One Do You Choose?
Choosing a testing method will depend on a few factors. They may include availability of the testing contractor, your budget, site conditions, and your plans for the building. If you know all the plumbing is old cast iron, hydrostatic testing only is probably a reasonable single test because regardless of the outcome you will probably be replacing it in the future anyway and you just want to know now if it is leaking. For all other situations choosing camera testing or a combination of camera and hydrostatic testing makes sense and your plumbing contractor or engineering inspection contractor can help you decide. Camera testing is strongly recommended if you have had drain repairs to detect poor quality and incomplete repairs, which sometimes occur and can affect drain and foundation performance. Testing should always be performed under the guidance of an engineer or licensed plumber.
When scheduling testing consider the other inspections you are having performed. Testing can interfere with a basic inspection of a building by a building inspector. It is best to arrange for testing before or after your building inspection if you are going to have them on the same day. Be sure to discuss this with your inspection contractor so they can help you plan your day. Give our office a call if you would like to discuss testing further, although we do not currently perform testing we can help you find a contractor or arrange testing as a part of our inspection services.
Recent Comments